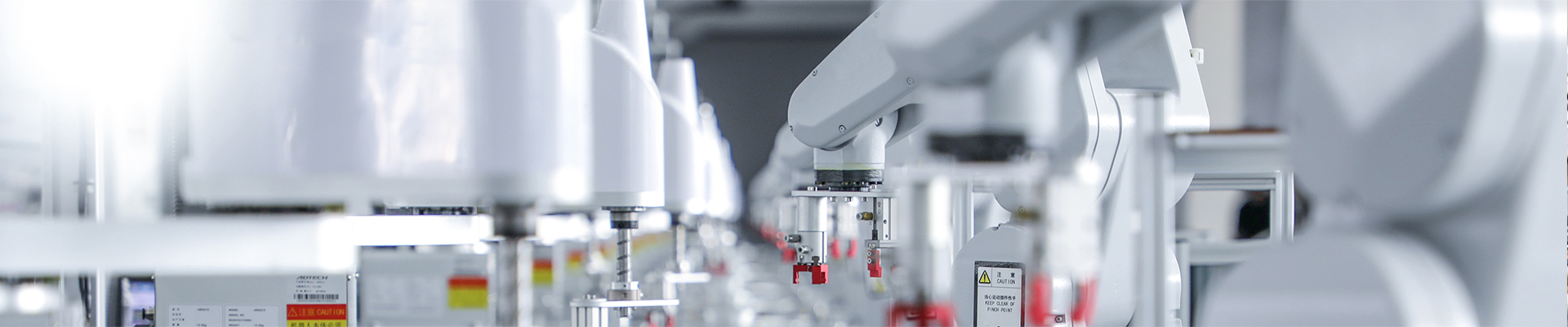
shell and tube heat exhcanger
2019-08-23 15:07Heat exchanger classification:
Shell-and-tube heat exchangers can be classified into the following two categories according to their structural characteristics.
1. Shell-and-tube heat exchanger with rigid structure: This heat exchanger has become a fixed tube plate type, which can be generally divided into single tube tube and multi tube tube. Its advantages are simple and compact structure, low cost and wide application; the disadvantage is that it can not be mechanically cleaned outside the tube.
2. Shell-and-tube heat exchanger with temperature difference compensation device: it can freely expand the heated portion.
This structural form can be further divided into:
1. Floating-head heat exchanger: One end of the heat exchanger can be freely telescoped, so-called "floating head". He is suitable for large temperature differences between the pipe wall and the shell wall, and the tube bundle space is often cleaned. However, its structure is more complicated and the cost of processing and manufacturing is higher.
2 U-tube heat exchanger: It has only one tube plate, so the tube can be freely stretched when heated or cooled. The structure of the heat exchanger is simple, but the workload of manufacturing the elbow is large, and since the pipe needs a certain bending radius, the utilization rate of the pipe plate is poor, the mechanical cleaning in the pipe is difficult, and the pipe is not easy to be replaced. It is therefore required that the fluid passing through the tube be clean. This heat exchanger can be used in applications where the temperature difference varies greatly, high temperature or high pressure.
Review of design conditions:
1. For the design of the heat exchanger, the user should provide the following design conditions (process parameters):
1 tube, shell operation pressure (as one of the conditions for determining whether the equipment is on the class, must be provided)
Operating temperature of 2 tubes and shell side (inlet/outlet)
3 metal wall temperature (process calculation (user provided))
4 material name and characteristics
5 corrosion amount
6 numbers of heating transfer
7 heat exchange area
8 heat exchange tube specifications, arrangement (triangle or square)
9 baffles or number of support plates
10 insulation material and thickness (in order to determine the extension height of the nameplate seat)
Material
Forgings should be used when the tube sheet itself has a shoulder and is connected to the cylinder (or head). Since the tube sheets adopting such a structure are generally used for occasions with high pressure, flammability, explosiveness, and extreme degree of toxicity, the tube sheets are required to be high and the tube sheets are thick. In order to avoid the occurrence of slag, delamination at the shoulder, and to improve the stress of the fiber at the shoulder, reduce the amount of processing, save materials, and use the integral forging directly forged by the shoulder and the tube sheet to manufacture the tube sheet.
Heat exchanger and tube plate connection
The connection of the tube to the tubesheet is an important structural part in the design of the shell-and-tube heat exchanger. He not only has a large amount of processing work, but also must make each connection in the operation of the equipment to ensure that the medium has no leakage and can withstand the pressure of the medium.
There are three main ways of connecting the pipe to the tube sheet: a expansion joint; b welding; c expansion welding
The expansion joint is used for the case where the leakage of the medium between the tubes does not cause adverse consequences, and is particularly suitable for the case where the weldability of the material is poor (such as carbon steel heat exchange tubes) and the workload of the manufacturer is too large. Due to the plastic deformation at the end of the expansion joint, there is residual stress, and the residual stress gradually disappears with the increase of temperature.
This reduces the sealing and bonding force at the end of the pipe, so the expansion joint structure is limited by pressure and temperature, and is generally suitable for design pressure ≤ 4Mpa, design temperature ≤ 300 degrees, and no violent vibration during operation, no excessive Temperature change and no obvious stress corrosion;
The welded connection has the advantages of simple production, high efficiency and reliable connection. Through welding, the pipe has a better effect on the tube sheet; and there are advantages such as reducing the processing requirements of the tube hole, saving processing time, convenient maintenance, etc., so it should be preferred.
In addition, when the medium is very toxic, the medium and the atmosphere are mixed. It is easy to cause the explosive medium to have radioactivity or the mixing of the materials inside and outside the tube may have adverse effects. In order to ensure the joint sealing, the welding method is also often used. Although the welding method has many advantages, it does not completely avoid "crevice corrosion" and stress corrosion of the welded joint, and it is difficult to obtain a reliable weld between the thin pipe wall and the thick pipe plate.
Although the welding method can be higher temperature than the expansion joint, under the action of high temperature cyclic stress, the weld joint is prone to fatigue crack, and there is a gap between the tube and the tube hole. When it is corroded by corrosive medium, it will accelerate the joint. Damage.
Therefore, a method of simultaneously using welding and expansion is produced. This not only improves the fatigue resistance of the joint, but also reduces the tendency of crevice corrosion, so its service life is much longer than that of welding alone. In any case, there is no uniform standard for the method of welding and expansion.
Generally, when the temperature is not too high and the pressure is high or the medium is extremely leaky, the strength expansion and sealing welding are used (sealing welding refers to welding performed by simply preventing leakage, and strength is not guaranteed). When the pressure and temperature are high, the strength welding is used to increase the expansion. (Strength welding is to ensure that the joint has a large pulling force even if the weld is tight, usually the weld strength is equal to the pipe. Welding at the strength under axial load).
The effect of swelling is mainly to eliminate crevice corrosion and improve the fatigue resistance of the weld.
For the surface roughness of the tube hole:
a When the heat exchange tube is welded to the tube sheet, the surface roughness Ra of the tube is not more than 35uM
b When the single heat exchange tube and the tube sheet are expanded and joined, when the surface roughness Ra of the tube hole is not more than 12.5uM, the surface of the tube hole shall have no defects affecting the tightness of the expansion joint, such as the longitudinal or spiral shape of the through hole. Scoring, etc.